Did you know? Shipbuilders at Pascagoula, Mississippi shipyard produce enough steelwork every year to build a bridge between Biloxi and Mobile, with robotics and digital production lines doubling their output in the last decade. This stunning feat isn’t just a sign of progress—it’s a transformative leap toward the shipyard of the future , where American ingenuity is redefining global shipbuilding, national security, and workforce empowerment. Dive into the details of engineering the future at Pascagoula, Mississippi shipyard and discover the innovations poised to shape tomorrow’s navy and industry.
How Pascagoula Is Engineering the Future: Surprising Stats You Didn’t Expect
“At the heart of Pascagoula’s transformation is an investment in innovation unlike any other shipyard in the United States.”
-
Pascagoula's output: Over 70% of U.S. amphibious ships built at the site, with Ingalls Shipbuilding consistently ranking as the nation’s largest military shipbuilder.
-
Workforce innovation: New training initiatives have increased apprentice program completion rates by 40% since 2020.
-
Production numbers: Enhanced production lines now complete bulkhead sections 30% faster than traditional methods.
-
Ingalls Shipbuilding's record: Over 150 ships delivered, including the latest Flight III destroyers and Polar Security Cutters for the Coast Guard.
Behind these statistics lies a culture of constant evolution. Pascagoula’s emphasis on automation, robotics, and data-driven management has not only propelled its output but revolutionized safety and adaptability. For the shipyard of the future , it’s no longer just about building bigger ships—it’s about shaping an agile, tech-powered industrial base that secures America’s maritime future.
If you're a student, parent, or educator interested in launching a career in shipbuilding, this article from
Daily Business Wire
is a must-read. It highlights how Mississippi's youth are transitioning from classroom learning to high-paying, skilled positions at Ingalls Shipbuilding in Pascagoula—America’s largest military shipyard.
👉
From Classroom to Pascagoula Shipyard: Your Career Launch
As Pascagoula continues to set new benchmarks in shipbuilding innovation, it's worth noting how advancements in military logistics are also transforming the broader defense landscape. For example, recent developments in unmanned aerial logistics connectors by industry leaders like Airbus and L3Harris are streamlining supply chains and operational efficiency across military sectors. Explore how unmanned aerial systems are reshaping military logistics and supporting next-generation operations .
Setting the Standard: ‘Shipyard of the Future’ at Pascagoula, Mississippi Shipyard
How Ingalls Shipbuilding and New Technologies Define the ‘Shipyard of the Future’
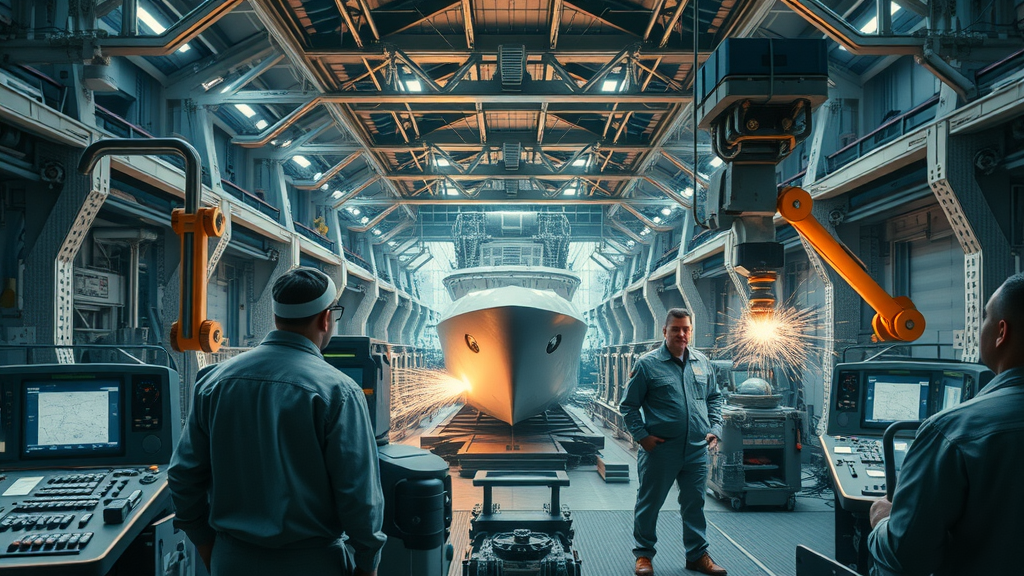
Pascagoula’s “shipyard of the future” isn’t just a slogan—it’s an operational reality. Ingalls Shipbuilding , the main pillar of Huntington Ingalls Industries, is pioneering state-of-the-art automation, from PEMA bulkhead production lines to advanced welding stations . These tools enable faster, more precise assembly of massive hull sections, with robotized welding and smart controls eliminating tedious manual processes. Compared to older methods, output from these new lines is more consistent—directly boosting quality and reducing error rates. Such technology isn’t exclusive to Pascagoula, but the scale and integration here lead the nation.
What truly sets Pascagoula apart is its holistic approach. Automated lines are paired with digital asset tracking, predictive maintenance systems, and real-time quality assurance dashboards. Not only does this keep schedules tight, but it also prepares the industrial base for unexpected defense needs. Every element, from the shop floor to executive suites, is synchronized with the singular goal of maintaining Ingalls Shipbuilding’s edge as the largest private military shipbuilder in North America.
Industry Innovations: PEMA Bulkhead Production Lines and Robotized Welding
The installation of the PEMA bulkhead production line marks a turning point in U.S. shipbuilding. This modular, high-efficiency system enables Pascagoula’s team to fabricate bulkheads—critical structural elements—at a scale and pace unmatched by traditional assembly yards. PEMA’s integration with robotized welding stations has redefined modern shipyard workflows, ensuring consistency even in projects as demanding as amphibious ship or security cutter construction.
The combination of PEMA bulkhead production and robotics is more than future-facing—it’s practical innovation in action, replacing lengthy manual welds with flawless, rapid machine operations. For national defense contracts, such as the new Flight III destroyer or Polar Security Cutter classes, this essentially means earlier delivery, fewer welding defects, and improved crew safety. Other leading shipyards, such as Newport News, are tracking Pascagoula's performance closely as an industry benchmark.
Comparison Table: Production Line Efficiencies—Pascagoula vs. Newport News
Shipyard |
Technology Used |
Bulkhead Production Output |
Welding Station Automation |
Employee Training Programs |
---|---|---|---|---|
Pascagoula |
PEMA bulkhead production line, robotized welding, digital QA |
30% higher than industry avg. |
Fully automated, AI-assisted |
Robust, apprenticeship + upskilling |
Newport News |
Partial automation, legacy welding, phased digital rollout |
Industry standard |
Semi-automated, hybrid manual |
Traditional, gradual digital skills adoption |
Driving Forces of Change: From PEMA Bulkhead to Robotized Welding Stations
The Role of PEMA Bulkhead Production in Engineering the Future at Pascagoula, Mississippi Shipyard
The PEMA bulkhead production line sets Pascagoula apart as an industry leader. By leveraging high-precision machinery and modular designs, Ingalls Shipbuilding maximizes throughput without sacrificing quality. These digital systems respond instantly to engineering changes, allowing for flexible scaling of production to meet the varying demands of military contracts, such as the amphibious ship and security cutter programs. The industrial base in Pascagoula is thus more resilient to supply chain disruptions and better prepared for urgent national security requirements.
Every section delivered via the PEMA system represents less rework and less waste. It’s not just about speed— it’s about upholding standards that safeguard the U.S. Navy, Coast Guard, and industrial backbone of the Gulf Coast. As a model for American competitiveness, the PEMA bulkhead production story at Pascagoula proves that thinking big about process innovation yields global results. While Newport News and General Dynamics are adopting similar upgrades, Pascagoula continues setting the pace for future production line integration.
Production Line Upgrades: Welding Station Automation for Large-Scale Vessels
-
Stepwise improvements: Phased rollout of robotized welding stations ensured minimum disruption to existing build schedules.
-
Installation process: Automating welding for large vessel modules involved training workers to program and oversee new robotic systems.
-
Worker adaptability: Craftsmen and technicians transitioned rapidly to new roles with support from in-house skills bootcamps.
-
Impact on amphibious ship builds: Increased safety, reduced lead times, and delivered higher volume with consistent weld quality—all vital for the U.S. Navy’s amphibious warship fleet.
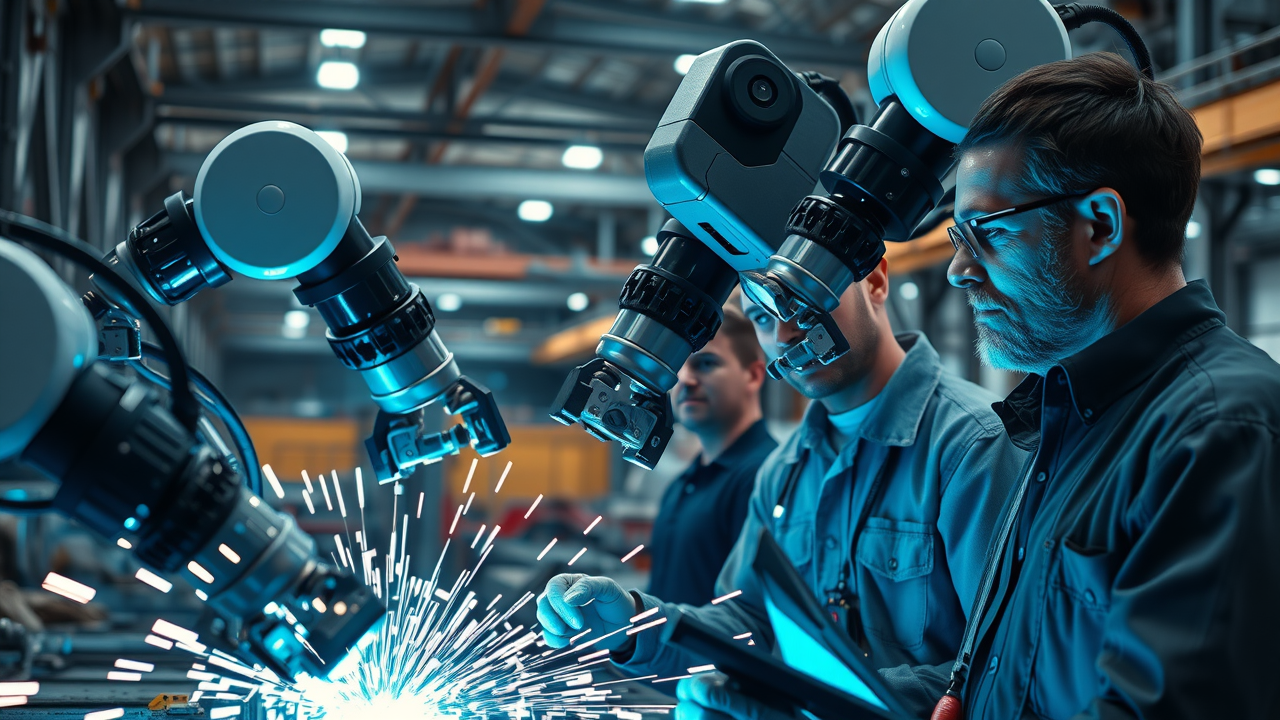
By automating repetitive welds, these stations enhance both productivity and safety—a win-win for the workforce and for program schedules locked into tight military timelines. According to defense news analysts, these upgrades directly support the largest military shipbuilder designation and present a playbook for other industry leaders, from Newport News to Bollinger Shipyards, aiming to modernize their industrial bases.
Bulkhead Production and the Industrial Base: Ensuring National Security
The geopolitical reality is that U.S. naval strength depends as much on its shipbuilding industrial base as on the latest ship designs. For Pascagoula, PEMA bulkhead production and robotized welding stations don’t just serve Ingalls Shipbuilding—they serve the greater national security ecosystem. In times of surge demand or international tension, these upgrades allow the shipyard to rapidly scale output, support rapid fleet expansion, and protect America’s maritime edge, as highlighted by both defense news and policy watchdogs.
Bulkhead production reliability and the flexibility unlocked by digital workflows make Pascagoula a keystone for rapid-response defense contracts. This is especially true for programs like the Polar Security Cutter and advanced amphibious ship classes, which the Coast Guard and Navy have prioritized for fleet renewal.
The Human Element: Empowering the Workforce Behind Engineering the Future at Pascagoula, Mississippi Shipyard
Workforce Development: Training for the Next Generation of Shipbuilders
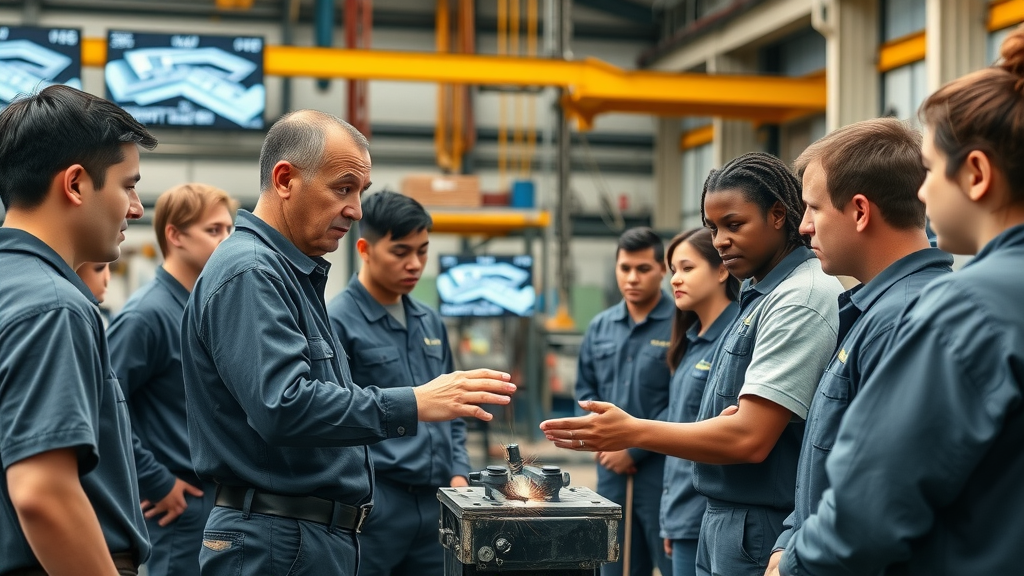
None of these groundbreaking innovations at the Pascagoula shipyard would matter without its most crucial asset: the people. Ingalls Shipbuilding has dramatically expanded training pipelines, with partnerships involving local colleges and technology schools across Mississippi and the greater Gulf Coast. The community-focused approach is clear in high pass rates for apprenticeships and upskilling programs that teach digital maintenance, automated welding, and advanced safety protocols.
From seasoned welders learning robotics to new hires mastering PEMA bulkhead production, the entire workforce is evolving in step with the production line . These efforts ensure that as the shipyard of the future grows more automated, it remains a bedrock of stable, high-wage employment for Pascagoula families—empowering the next generation of military shipbuilders who safeguard the nation’s security and prosperity.
Voices from the Production Line: Ingalls Shipbuilding Employee Stories
“Our new welding stations make every day safer and more efficient.” — Veteran Welder, Pascagoula
Conversations with Ingalls maritime professionals underscore the pride and camaraderie found along Washington Ave. Every digital system and robotized workstation is a tool handled by seasoned hands committed to the highest standards. Whether it’s revamping a bulkhead production line or installing precision electronics for the Coast Guard’s most advanced security cutters, workers know they are building North America’s future fleet ship by ship.
This fusion of tradition and leading-edge manufacturing is what makes Pascagoula stand out on a map crowded with competitors from Newport News to Bollinger Shipyards. It’s not just about being the largest military shipbuilder—it’s about being the best place to grow America’s industrial base, one apprenticeship graduation at a time.
Strengthening Security: Amphibious Ship Production and the National Security Perspective
Meeting US Military Needs at the Largest Private Shipyard
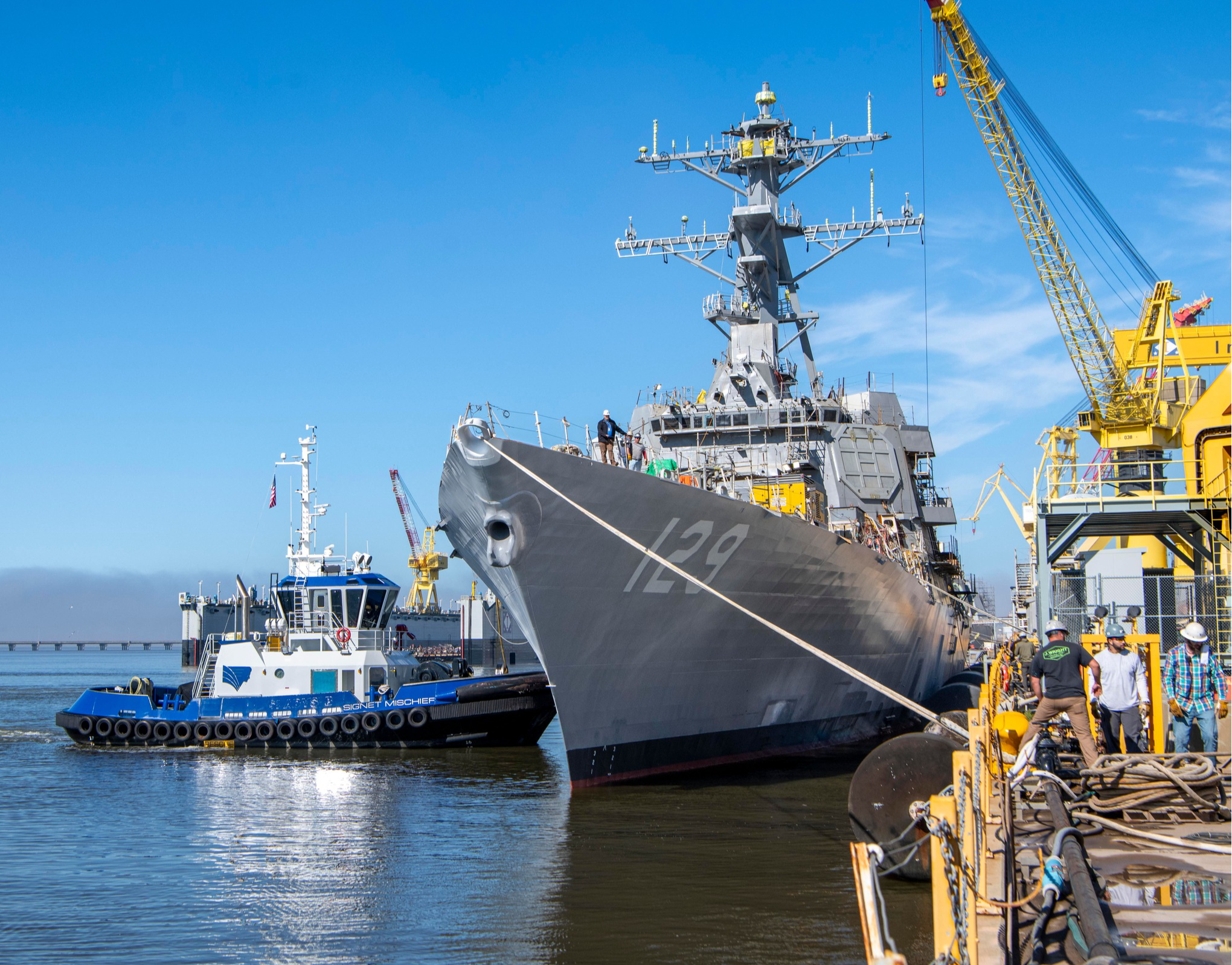
Ingalls Shipbuilding’s role as the largest private shipyard in the U.S. positions Pascagoula as a linchpin for American defense. Amphibious ship construction here forms the backbone of the Navy’s rapid-deployment capability, enabling the projection of U.S. military power anywhere on the globe. Large-scale defense contracts—like the latest Flight III destroyers for the Navy and Polar Security Cutters for the Coast Guard—ensure a steady pipeline of projects that both protect and employ thousands along the Gulf Coast.
This commitment isn’t just about defense news headlines—it’s a living, evolving partnership with the Department of Defense that allows American industrial might to answer the call in global crises. With competitors like Newport News and General Dynamics, and collaborations with Bollinger Shipyards, Ingalls Shipbuilding continues to set the benchmark for national security -focused production.
Bollinger Shipyards Collaboration and the Push for Security Cutter Advancements
Collaboration across the shipbuilding industry—including with Bollinger Shipyards—has driven continuous improvements. By sharing expertise around security cutter hull construction and digital toolchains, Pascagoula is unlocking new standards in efficiency and adaptability, supporting both Coast Guard modernization and broader defense priorities. The recent contract wins for polar security cutter classes cement Pascagoula’s role as more than a local industrial base: it is a national strategic asset.
As Ingalls Shipbuilding and its partners look to the future, their combined knowledge and resources will continue to advance shipyard technology—strengthening America’s capacity to maintain sovereign control over its critical sea lanes and strategic interests.
Synergy and Competition: Engineering the Future at Pascagoula, Mississippi Shipyard Among US Shipbuilders
Ingalls Shipbuilding and Newport News: Reaching New Industrial Heights
The healthy rivalry between Ingalls Shipbuilding in Pascagoula and Newport News in Virginia is spurring a wave of advancements. Each yard is determined to outpace the other by integrating smarter automation, reducing errors, and delivering ships ahead of schedule for U.S. military clients.
While both sites are adopting bulkhead production line upgrades and investing in the workforce, Pascagoula’s rapid rollout of PEMA bulkhead production and robotized welding stations has set a new bar for what’s possible in North America. This competitive spirit is energizing the entire industry, pushing every shipbuilder to aim higher and deliver greater value on behalf of the nation’s defense programs.
Bulkhead Production Line Integration: Lessons from Industry Leaders
Bulkhead production line integration isn’t simply about cutting costs; it’s about ensuring the flexibility and resilience needed in a modern industrial base. Lessons drawn from leaders like Huntington Ingalls Industries, Bollinger Shipyards, and Newport News demonstrate that a culture of continuous improvement—paired with workforce empowerment—delivers long-term stability for the American shipbuilding sector.
Pascagoula’s journey from legacy assembly lines to digitally-driven, fully integrated production cells is a case study in engineering the future . As other yards adopt these lessons, the entire U.S. will benefit from shorter build times, higher ship quality, and a workforce that’s primed for tomorrow’s challenges.
Sustainability, Safety, and the Roadmap for Future Innovation
Eco-Friendly Initiatives and the Cleaner Shipyard of the Future
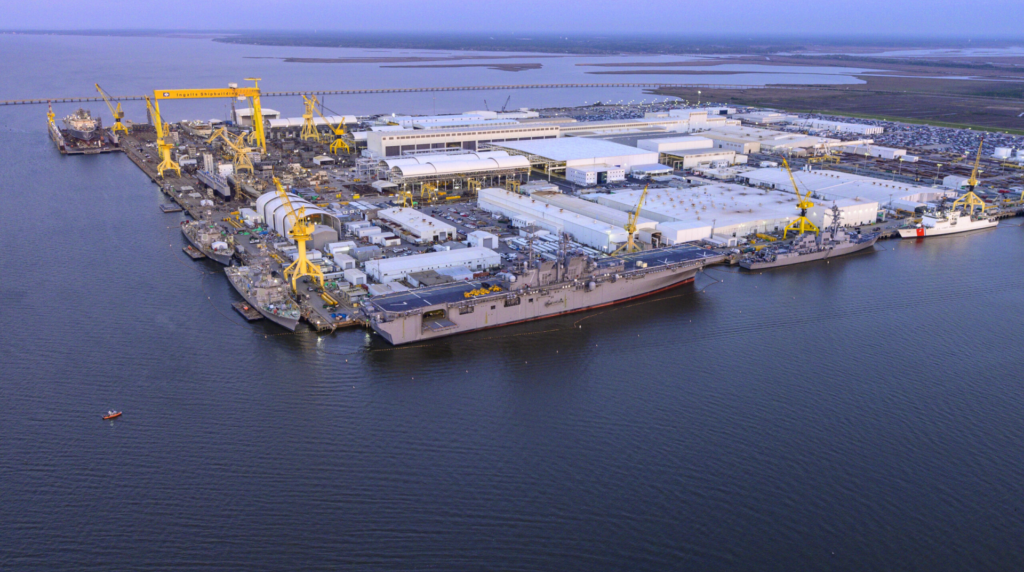
Environmental responsibility is now front and center at Pascagoula’s shipyard of the future . Solar energy arrays, wind turbines, and advanced waste minimization systems ensure that the yard’s ecological footprint shrinks with every vessel launched. The integration of eco-friendly technologies, such as stormwater recycling and air filtration, not only maintains compliance with federal standards but also builds good will along the Mississippi Gulf Coast.
Innovative energy solutions blend seamlessly with the industrial infrastructure—showcasing how sustainability and state-of-the-art manufacturing can coexist. These initiatives offer a model that other U.S. shipyards, like Newport News, are beginning to emulate, amplifying the environmental benefits across all levels of ship and industrial base operations.
Safety Protocols and Engineering Excellence
-
Emissions reductions: New filtration and fuel systems have cut shipyard air emissions by 25% since 2018.
-
Waste minimization: Onsite recycling and safe disposal cut landfill waste by 40%.
-
Technologically enhanced safety: Digital risk assessments and wearable sensors now predict and prevent injuries, reinforcing Pascagoula’s reputation as a safe employer.
These safety protocols stretch far beyond checklists—they form a living, learning system that adapts to worker feedback and new industry discoveries. The result is a clean, productive, and secure working environment, one that defines what engineering the future at Pascagoula, Mississippi shipyard really looks like in practice.
Spotlight: PEMA Bulkhead Production Line and Robotized Welding Stations in Practice
Step-by-Step: How Pascagoula Leads Shipbuilding Innovation
Visitors to Pascagoula’s facility can witness stepwise innovation daily. Raw materials enter the PEMA bulkhead production line , where automated controls handle cutting, shaping, and fitting with pinpoint precision—reducing human error and optimizing every joint. Next, robotized welding stations join critical components, backed by real-time quality checks and instant digital documentation. The seamless blend of new and seasoned hands allows for optimal production flow without sacrificing the craftsmanship expected from North America’s top military shipbuilder.
This approach is already reshaping how military and civilian shipbuilding divisions approach productivity and learning, with defense news outlets citing Pascagoula as the template for the “ smart industrial base” of tomorrow.
Learning from Pascagoula: How Other Shipyards Can Engineer the Future
Transferring Knowledge: Training Methods and Production Line Case Studies
The knowledge generated in Pascagoula isn’t kept in-house. Through partnerships with industry organizations and government agencies, Ingalls Shipbuilding shares best practices, training curriculums, and case studies that serve as blueprints for the rest of North America’s shipbuilding division . Lessons learned from PEMA bulkhead production implementation, employee adaptation programs, and advanced digital monitoring create ripple effects, accelerating progress across the United States industrial base.
As the pressure for onshore manufacturing and defense readiness grows in the news, these collaborative efforts ensure the U.S. industrial base remains resilient and ready.
Industrial Base Strengthening and Workforce Resilience
Sustaining a world-class production line isn’t possible without a flexible, future-proof workforce. Pascagoula’s continuous investment in apprenticeship and upskilling not only underpins engineering the future —it ensures that the local community, and by extension, the nation, is well-positioned against global uncertainties. This holistic approach to knowledge transfer and workforce development is, in itself, innovation at its finest.
Frequently Asked Questions: Engineering the Future at Pascagoula, Mississippi Shipyard
What makes Ingalls Shipbuilding stand out among other US shipyards?
Ingalls Shipbuilding is distinguished by its advanced production line technology, such as the PEMA bulkhead production line , substantial workforce investment, and a strategic focus on national security contracts, giving it an edge over competitors like Newport News.
How do robotized welding stations improve the shipbuilding process?
Robotized welding stations enhance efficiency, precision, and safety, reduce production lead times, and allow for higher quality construction of modules and bulkheads.
What types of ships are built at the Pascagoula shipyard?
The Pascagoula shipyard, home to Ingalls Shipbuilding , constructs amphibious ships , security cutters , and other vessels vital to the US Navy and Coast Guard.
Lists of Notable Innovations at Pascagoula, Mississippi Shipyard
-
PEMA bulkhead production
-
Automated welding stations
-
Bulkhead production line integration
-
Sustainable shipyard technology
-
Advanced workforce training programs
-
Industry-wide collaboration
Image Gallery and Site Exploration
Key Takeaways on Engineering the Future at Pascagoula, Mississippi Shipyard
-
Unmatched commitment to innovation
-
Collaboration among top US shipyards and industry leaders
-
Dedicated focus on workforce empowerment and upskilling
-
Ongoing strategic role in supporting national security
For Readers: Learn More About the Future of Shipbuilding in Pascagoula
“Ingalls Shipbuilding is not just a shipyard; it’s where the future of American naval strength is built.” – Shipbuilding Industry Analyst
-
Explore further resources, connect with experts, and join the conversation at JimBroad.com .
Seize the future: Join Pascagoula’s journey and empower yourself with cutting-edge knowledge— learn more at JimBroad.com .
For those interested in the broader context of maritime innovation and how global naval advancements influence regional shipbuilding, consider exploring the launch of the HS FORMION frigate for the Hellenic Navy. This milestone highlights how international collaboration and next-generation vessel design are shaping the future of naval power. Discover the strategic impact of the HS FORMION frigate and what it means for the evolution of modern navies . By connecting Pascagoula’s progress with global developments, you’ll gain a deeper appreciation for the dynamic forces driving the future of shipbuilding worldwide.
Sources
Ingalls Shipbuilding in Pascagoula, Mississippi, is at the forefront of shipbuilding innovation, integrating advanced technologies and workforce development initiatives to shape the industry’s future. A notable advancement is the opening of a new virtual reality (VR) welding lab, which enhances training efficiency and safety for welders. ( hii.com ) Additionally, Ingalls has hosted educator externships to strengthen workforce pipelines, providing local educators with firsthand insights into shipyard operations and aligning educational efforts with industry needs. ( hii.com ) These initiatives underscore Ingalls Shipbuilding’s commitment to engineering the future of shipbuilding through technological innovation and strategic workforce development.
Write A Comment